
Designing Commercial Laundry Facilities: A Guide for Architects, Contractors, and ConsultantsDesigning Commercial Laundry Facilities: A Guide for Architects, Contractors, and Consultants
In 2025, the demand for well-designed, compliant, and efficient commercial laundry facilities is rising-across sectors such as hospitality, healthcare, and multi-residential developments. For architects, building contractors, and consultants, the challenge is not only to meet legal and operational requirements but also to deliver spaces that are future-proof and cost-effective.
Wavepoint Group partners with project teams nationwide, offering specialist design services that ensure commercial laundry facilities are seamlessly incorporated into new builds and refurbishments. Our in-house engineers work closely with all stakeholders, supporting quality, speed, and robust after-sales support from concept to completion. We’ve put together this guide for architects, contractors and consultants to help them in the planning process.
Why Specialist Laundry Design Matters
Commercial laundry design is a specialist field. Unlike standard utility rooms, laundry spaces must accommodate heavy-duty equipment, complex utility requirements, and stringent hygiene standards. Early, expert-led design ensures:
- Compliance with health, safety, and building regulations
- Efficient workflows that minimise bottlenecks and downtime
- Optimised use of space, utilities, and resources
- Reduced risk of costly redesigns or retrofits
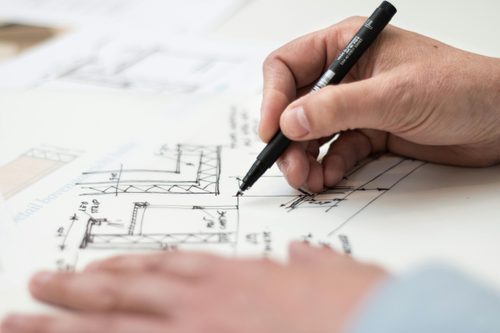
Core Considerations Checklist for Architects and Contractors
Designing a commercial laundry facility involves a series of interconnected decisions. Each project is unique, but the following areas are essential to address early, ideally with input from all stakeholders.
1. Location & Access
- Access issues are of concern when designing new laundries – can you get the machines in without costly machinery strip downs? Where is the laundry to be located – near the areas of demand / workflows? Drainage and ventilation issues?
- How close is the laundry area to external walls? Proximity can make ducting and ventilation more straightforward, and whether there’s enough uninterrupted wall space for tall dryers or stacked units and also for laundry storage and processing areas
- What about access for installation, daily operations, and future maintenance? Are there clear routes for moving equipment and laundry carts, and could separate entry points for clean and soiled laundry improve workflow?
2. Space Planning & Workflow
- Have you mapped out the equipment footprint, including necessary clearances for doors, panels, and service access?
- Does your layout allow for efficient movement between washing, drying, folding, and storage
- Would separating clean and soiled zones make sense for your client’s needs and compliance requirements?
- Is there enough space for both current operations and potential future expansion?
- Could dedicated storage areas outside the main laundry reduce clutter and improve workflow?

3. Equipment Selection & Integration
- What is the expected daily workload, and how will it be divided among machines? Will you opt for a few large-capacity washers or several smaller units for redundancy and flexibility?
- Are there any special requirements for linen type, finishing equipment, or automation? How might these choices affect space, utilities, and staffing?
- At what stage will you finalise equipment specs? Early decisions here can streamline utility planning and avoid costly redesigns down the line.
- Are there environmental targets or regulations influencing your equipment choices? For instance, would wet cleaning-using water and biodegradable detergents-be preferable to traditional dry cleaning, which relies on solvents like perc?
Many businesses are now prioritising energy and water efficiency, lower emissions, and reduced chemical use in line with the UK’s Net Zero ambitions.
4. Utilities & Technical Requirements
- Have you coordinated with M&E consultants to plan for plumbing, electrical, gas, drainage, and ventilation needs based on your chosen equipment?
- How will you address ventilation and humidity control, especially in high-volume facilities? Are your HVAC and plumbing systems designed to handle the demands of commercial laundry operations?
- Are utility service points accessible for installation and future upgrades?

5. Health, Safety & Compliance
- Which regulations-local, national, or sector-specific-apply to your project? Are you confident your design will meet all relevant hygiene, fire safety, and accessibility standards?
- Have you considered safe chemical storage, ergonomic layouts, and infection control measures, particularly in healthcare or hospitality settings?
- Is your facility designed to keep clean and soiled items separate, minimising the risk of cross-contamination?
6. Future-Proofing & Flexibility
- Is your design adaptable for future changes-in workload, equipment, or workflow? Would modular layouts or scalable utilities help accommodate evolving needs?
- How easy will it be to service or replace equipment as technology advances? Are you building in enough sustainability features, such as energy- and water-efficient machines, to meet both current and future expectations?
Every decision in these areas can have a knock-on effect elsewhere in the project. By considering these questions and steps early, you can create a commercial laundry facility that is not only compliant and efficient, but also resilient and ready for whatever the future brings.
The Value of Early Equipment Specification
A critical-but often underestimated-factor in achieving these outcomes is the early selection and specification of laundry equipment.
Specifying the right washers, dryers, and finishing equipment at the earliest design stages is essential for several reasons:
- Space Planning: Equipment footprints, access routes, and service zones can be accurately incorporated into layouts, avoiding clashes and last-minute changes.
- Utility Coordination: Early selection allows for precise planning of electrical, water, gas, drainage, and ventilation needs, ensuring M&E (mechanical and electrical) systems are right-sized from the outset.
- Compliance and Safety: Many projects require equipment that meets specific standards (e.g., WRAS approval, infection control, fire safety). Early engagement ensures all regulatory requirements are met.
- Operational Efficiency: The right equipment mix-matched to projected workloads-maximises throughput, energy efficiency, and ease of maintenance.
- Procurement and Lead Times: Early decisions help avoid supply chain delays and support smoother project timelines.
Wavepoint Group’s design team brings deep expertise to this process, guiding clients through equipment evaluation, lifecycle cost analysis, and suitability assessments to ensure optimal choices.
By engaging with Wavepoint’s specialists at the concept stage, project teams can:
- Ensure the facility is fit for purpose from day one
- Avoid costly rework and delays
- Achieve operational efficiency and long-term value
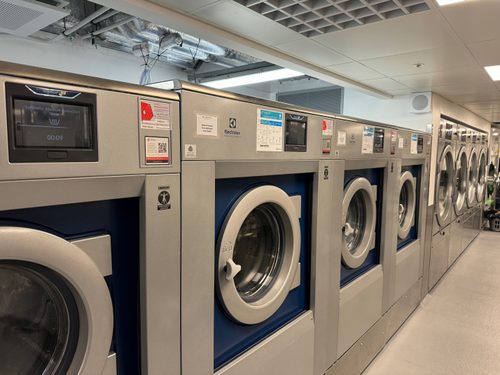
Wavepoint Group’s Collaborative Design Process
Our approach is built around close collaboration with architects, contractors, and consultants at every stage:
Stage | How Equipment Selection is Integrated |
Design Consultation | Assess operational needs, recommend suitable equipment types and capacities, and align with project goals. |
Tender Proposals | Provide detailed equipment specifications for accurate pricing and competitive procurement. |
CAD Drawings & Plans | Incorporate selected equipment models, ensuring layouts reflect real-world space and utility needs. |
Construction Drawings | Finalise documents with confirmed equipment, reducing installation risks and streamlining handover. |
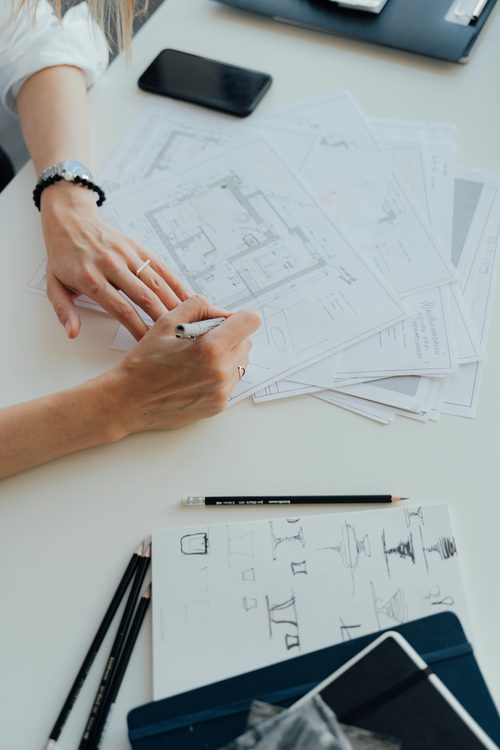
How to Get Started
Wavepoint Group welcomes early engagement with architects, contractors, and consultants. Our design team offers:
- No-obligation consultations to discuss project requirements
- Equipment recommendations tailored to your operational needs
- Support with tender documentation, CAD layouts, and construction drawings
Benefits of working with Wavepoint Group:
- In-house engineering expertise: Tailored solutions for each project’s unique requirements.
- Fast turnaround: Rapid design and support during installation.
- After-sales support: Ongoing performance checks and compliance advice.
- Advanced technologies: Integration of energy-efficient and sustainable laundry solutions.
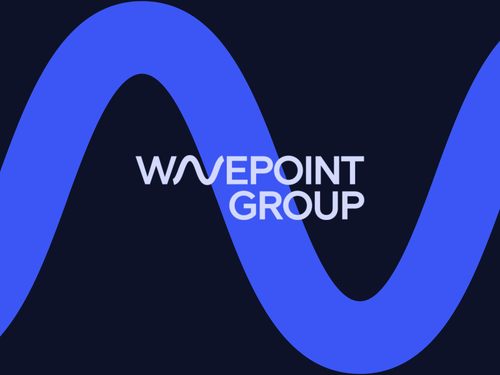
Conclusion
The success of commercial laundry facilities hinges on early, expert-led design and equipment specification. By partnering with Wavepoint Group from the outset, architects, contractors, and consultants can deliver laundry spaces that are compliant, efficient, and built to last.
Contact Wavepoint Group today to discuss your next project and discover how our design services can add value from concept to completion.
Latest articles

Financing Commercial Laundry Finishing Equipment: Lease vs. Buy
Acquiring new commercial laundry finishing equipment is a significant step for any UK business looking to…
Read more
How to Choose the Right Laundry Finishing Equipment for Your Business
Investing in commercial laundry finishing equipment is a big decision for any UK business. Whether you run a…
Read more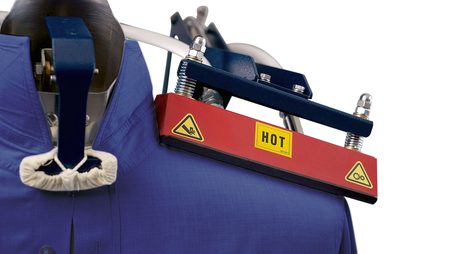
Types of Commercial Laundry Finishing Equipment and Their Uses
In our previous guide, we explored what laundry finishing is and why it matters for businesses across the UK.…
Read more